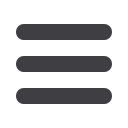
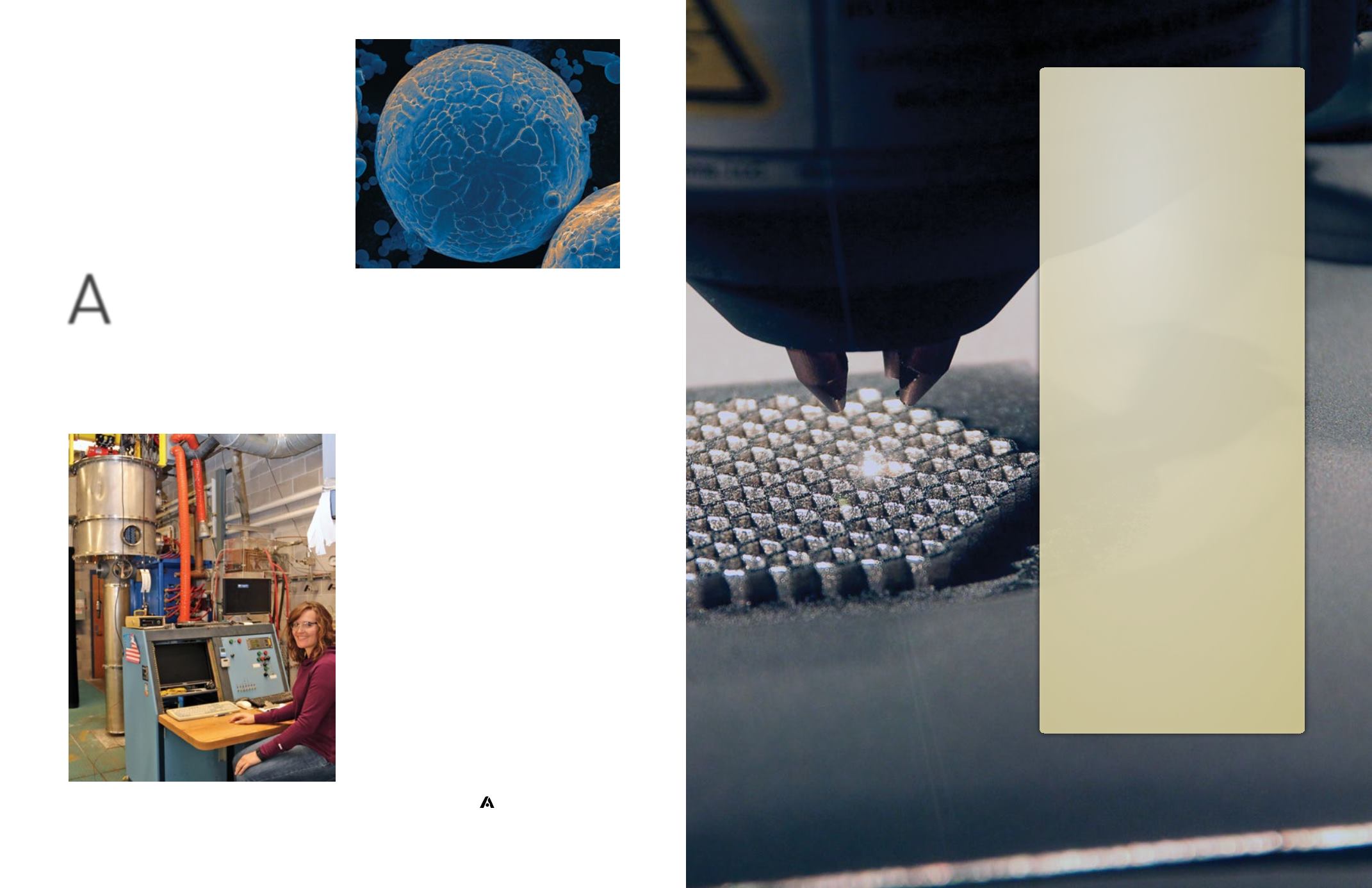
Ames Laboratory’s LENS system creates complex, 3D shapes by depositing metal
powders through the nozzles and simultaneously melting them with a laser.
12
Inquir y I s sue 2 | 2016
Inqui ry I s sue 2
|
2016
13
dditive manufacturing, also known as 3D
printing, has reached a widespread measure
of success in manufacturing processes using
polymers, or plastics. But the use of metal alloys
for additive manufacturing has lagged due to lack of both
materials and process development.
Ames Laboratory and Oak Ridge National Laboratory
have been awarded $5 million from the U.S. Department of
Energy’sAdvancedManufacturing Office (AMO) to improve
the production and composition of metal alloy powders used
in additive manufacturing.
“There’s a lot of intense interest focused on additive
manufacturing with metal alloys, because there are so many
potential applications,” said Iver Anderson, project leader
and senior metallurgist at Ames Laboratory and adjunct
professor of Materials Science and Engineering at Iowa
State University. “Industry has demands for prototyping
parts, design development, reducing waste of expensive
materials, and efficiently producing custom and legacy
components for their customers.”
Because additive manufacturing uses metal alloy powders
as its raw material, the ability to control the properties and
quality of those powders becomes paramount to the quality
of the final product, and achieving properties equal to cast
and machined or, especially, cast/forged and machined parts.
The project will improve powder production by developing
advancesinahigh-pressuregasatomizationprocesspioneered
at Ames Laboratory and will design and customize alloys
specifically for additive manufacturing processing methods.
Modeling and simulation of gas atomization process stages at
Ames Laboratory will use a flow simulation code developed
by the National Energy Technology Laboratory for part of
the work. The experimental gas atomization work and alloy
design calculations/verification also will be performed in
the powder synthesis facilities at Ames Laboratory. Oak
Ridge National Laboratory’s Manufacturing Demonstration
Facility (ORNL-MDF) will conduct the corresponding
additive manufacturing experiments.
“Today, if a manufacturer went to metal powder producers
with a shopping list of the alloys and powder specifications
they needed for their manufacturing process, they very
likely wouldn’t find what they want,” said Anderson. “The
customization capabilities are just not there, and we need
to get there. That is going to be the key to commercially
competitive additive manufacturing processes.”
B Y L A U R A M I L L S A P S
A
A micrograph shows the perfectly spherical shape of powder
particles formed by high-pressure gas atomization (HPGA).
Better Powders
AdvanceAdditive
Manufacturing
Ames Laboratory scientist Emma White sits at the control
panel for one of Ames Laboratory’s HPGA systems.
In a separate, but somewhat related project,
a group of Ames Laboratory researchers will be
working to characterize what happens to metal
powders as they are processed into shapes through
3D printing processes. The goal is to be able to fine-
tune the 3D printing process on the fly to maximize
the properties desired for the particular piece being
manufactured.
Ames Laboratory scientists Ryan Ott, Pete
Collins and Matt Kramer will be working with
colleagues at the Stanford National Accelerator
Laboratory (SLAC) and Lawrence Livermore
National Laboratory (LLNL) to develop both
hardware and software to characterize the powders
in situ
as the advanced manufacturing process
builds up complex shapes layer-by-layer.
“We’ll look at analyzing powders in two types of
systems, both powder feed and powder bed,” said
Kramer, who is also Ames Laboratory’s Materials
Science and Engineering program director. “Powder
feed is like our LENS (laser engineered net
shaping) system where powders are delivered via a
nozzle and melted in place by a laser. Powder bed
spreads a thin layer of the metal powders over the
entire surface and a laser then melts only a portion
of the powders in the particular shape needed.”
The Ames Laboratory team is characterizing the
commercial powders and developing the power feed
system that can be used with the beam line at SLAC
to analyze the powders as they are built up layer by
layer via X-ray tomography and diffraction. LLNL
is developing the powder bed system and high-
speed imaging and thermal diagnostics. According
to Kramer, the project will evaluate a wide range
of commercial powders, including a titanium-
aluminum-vanadium alloy commonly used in the
aerospace industry. Funding for the project will
come from DOE’s Advanced Manufacturing Office
with Ames Lab receiving roughly $1.2 million of
the approximately $4 million project.
Characterizing powders on the fly