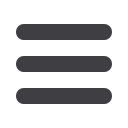
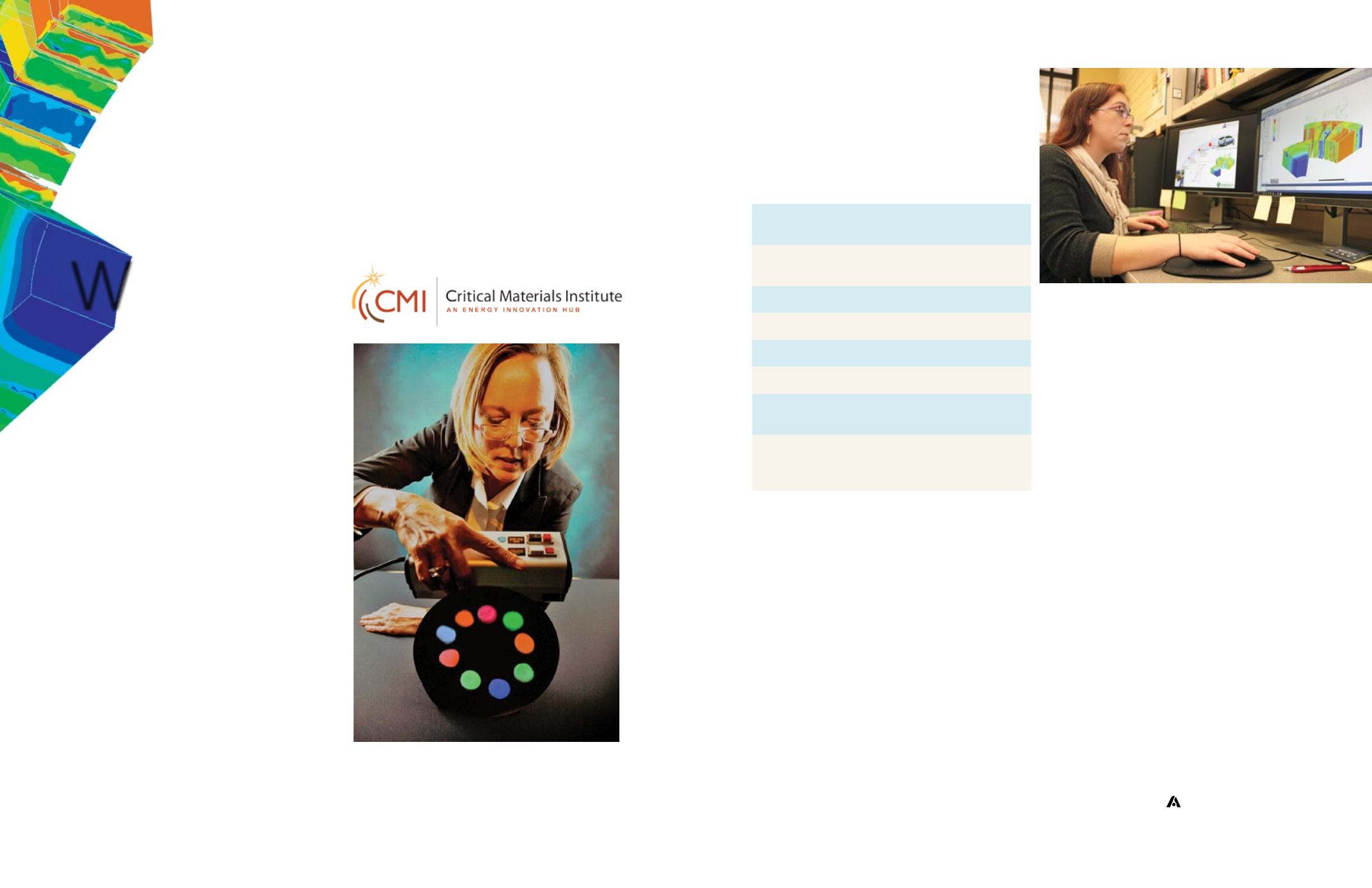
14
Inqui r y I s sue
2
| 2016
Inqui r y I s sue
2
| 2016
15
hen the Critical Materials Institute
(CMI) launched in 2013, it had an audacious
mission. It was not only charged with
developing technologies that could diversify,
substitute, or recycle rare-earth metals and
other materials critical to the nation’s clean
energy security; the DOE energy innovation
hub needed to do it fast. Mind-bogglingly fast, as a
matter of fact, considering that the traditional timeline
to deployment of a new material or process is usually 18 to
20 years.
“At the time, I had complete faith in the abilities of the
researchers we brought together. They truly were the best
and the brightest at what we’re doing here,” said CMI
Director Alex King. “But it was unknown whether we could
really work as a team, get sufficient buy-in from industry
leaders and move quickly enough to get where we needed
to go.”
A little over three years, 47 invention disclosures, and
multiple industry partnerships later, the hub has been
basking in the DOE’s and legislators’ praise. Part of the
secret, King said, is a combination of computational theory,
high through-put experimentation, and close collaboration
with industry partners.
“A great deal of our progress hinges on deciding what not
to do,” King said. “Abandoning ideas that are impractical,
too time-consuming, too expensive, or of too little interest
to industrial partners, who are the people who take the
research from the lab bench and actually make it go.”
Tom Lograsso, one of four research team leaders at CMI
and Ames Laboratory’s deputy director, agrees that the right
methodology has proven successful, using just one example
from his own research team.
“I think we’ve demonstrated the use of tools that allow us
to be highly responsive, and phosphors are my poster child
for that,” Lograsso said. “We went from having no substitutes
to having two green and one red phosphor for long tube
fluorescent lighting. We discovered which phosphors have
not only the appropriate fundamental properties, but also
the manufacturing characteristics that allowed them to be
currently in manufactured products. To do this all in slightly
more than three years is phenomenal, and we’ve now got a
stretch goal to find red and green phosphors for LED lighting
within the next two years.”
With a just a little under two years left in CMI’s 5-year
funding cycle, the DOE asked the hub to challenge itself
even further, and its researchers responded with eight new,
more specific and more challenging goals.
§
Produce a neodymium-iron-boron magnet using
materials and technologies located entirely within the
United States.
§
Discover a new permanent magnet that rivals
neodymium-iron-boron magnets in performance, using
reliably available elements.
§
Develop a commercial product based on an aluminum-
and cerium-based casting alloy.
§
Develop a working, inexpensive, bulk-scale, exchange-
coupled spring magnet.
§
Design a new permanent-magnet motor with
optimized system performance.
§
Discover new red and green phosphor candidates
suitable for use in LED lamps.
§
Demonstrate hard disc drive disassembly rates
exceeding 5,000 per day, to speed recovery of magnets
for recycling or re-use.
§
Scale up the supercritical fluid process for dissolution,
separation of dissolved components, and refinement of
separated critical elements, from milligram to kilogram
quantities.
Of these, King mentioned in particular the challenge
of developing an exchange-coupled spring magnet, a
theoretical idea in which two different magnets are
combined at the nanometer scale that creates a magnet with
the best properties of both, rather than just their average.
While they’ve been created in the lab on a small scale, CMI
proposes to create ones that could be made on a bulk scale
and large enough for applications like motors.
“That’s going to be a hard one, no doubt about it, but we
believe we have some insight now with our three years of
research experience that will help guide us in pursuit of this
goal,” said King.
Other magnet discoveries remain in this list of goals as
well, including new permanent magnets that use less critical
materials.
“To find a new magnet that rivals the most powerful
magnet is a challenging task; it’s been 45 years since NdFeB
magnets were discovered,” said Lograsso. “If it was easy,
we would have had something by now. But we have some
promising leads on magnets that may fill a gap between
weaker magnets and the most powerful ones, applications
where we’re currently using stronger magnets than we need
to be. We are also working on refining the processing of
magnetic materials we already do have, through things like
additive manufacturing and magnetic field treatments.”
Another notable goal takes CMI in a slightly new
direction, designing a new permanent magnet motor.
“We are asking ourselves: if we could make a magnet any
shape we want, what kind of motor could we design with it?”
said King. “It’s a matter of combining magnet design with
motor design, instead of treating them as entirely separate
challenges.”
“It’s taking the design of magnets to the systems level,
so it’s more of an engineering goal rather than fundamental
science, but it’s completely in keeping with CMI’s goals,”
said Lograsso.
King and Lograsso both consider the new goals high-risk,
but ultimately obtainable.
“We took a hard look at where we’ve been, and the places
we’re most likely to cross the finish line in the time left,
and from there we developed these more specific goals,”
said King. “We believe with industry informing our research
decisions, we’ve got the right strategy to meet success.”
B Y L A U R A M I L L S A P S
Early successes lead to new and bigger challenges
CriticalMaterials Institute:
W
CMI researcher Nerine Cherepy, from Lawrence Livermore
National Laboratory, displays phosphors developed to use far
less rare-earth oxides than in current fluorescent lighting tech-
nology. CMI researchers’ next goal is to develop red and green
phosphors for LED lighting.
Postdoctoral researcher Helena Khazdozian reviews a
technical presentation on permanent magnet motor design.
One of CMI’s eight research goals aims to integrate permanent
magnet development with motor engineering design as a
means of optimizing both.
“It’s taking the design of magnets to the
systems level,so it’s more of an engineering
goal rather than fundamental science,but
it’s completely in keeping with CMI’s goals.”