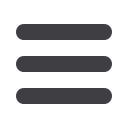
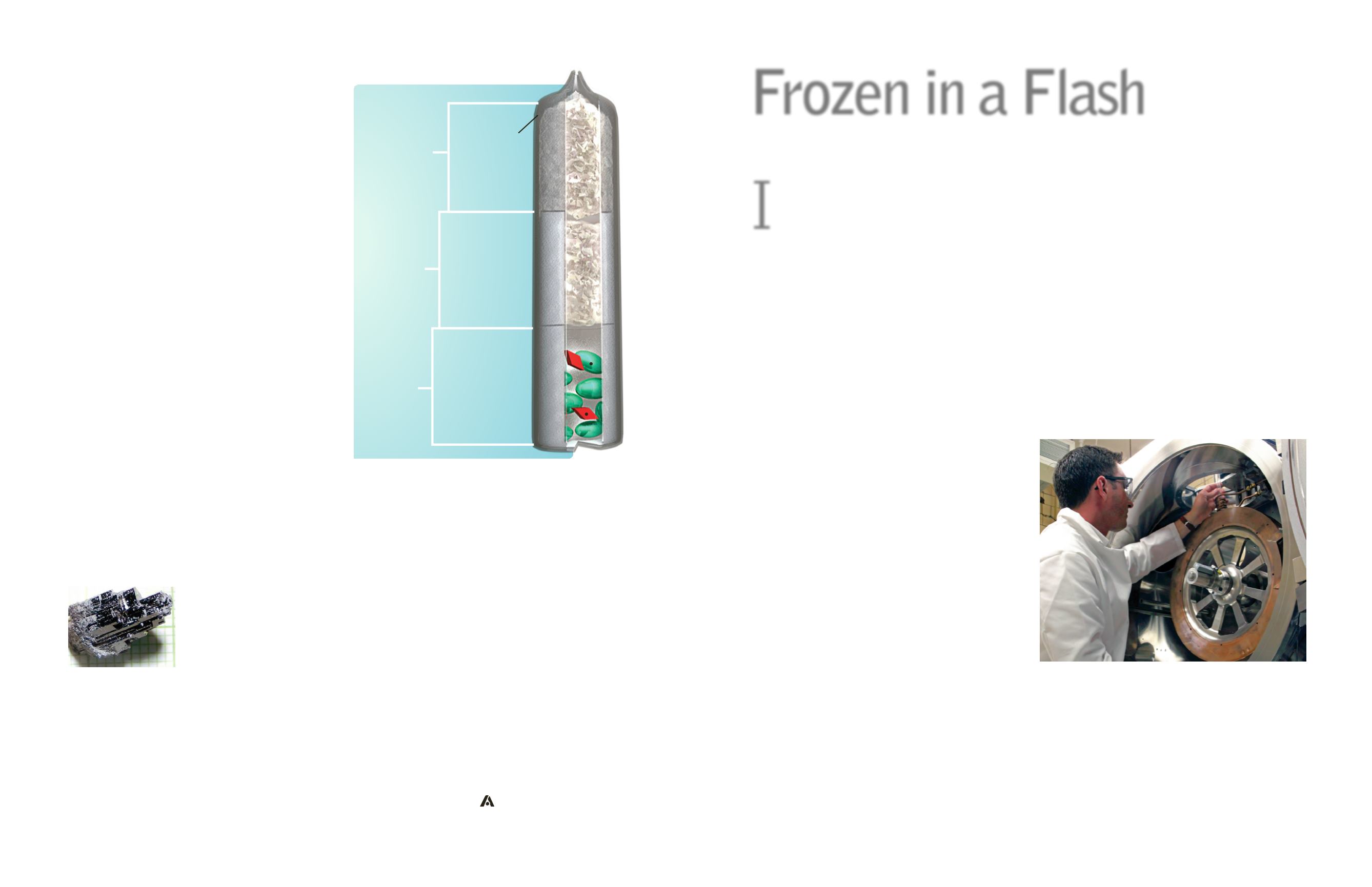
10
Inquir y Is sue
1
| 2016
Inquir y I s sue
1
| 2016
11
To then separate the liquid tin from the Ce-Sb crystal, the
tube assembly is removed from the furnace and immediately
placed in a centrifuge, which spins the remaining liquid
tin off into the catch crucible, leaving the crystal behind.
The centrifuge delivers up to 100 times the force of simple
gravitational decanting, resulting in “cleaner” crystals.
“When you develop new materials, you need to have
some familiarity with the ingredients and the techniques
at hand,” said Canfield. “With solution growth, we can go
from looking at superconductors and ferromagnets, to spin
glasses, to quasicrystals—go from one material to another to
another—just by changing elements or growth conditions.
Over the course of 20 years here, we are closing in on 10
thousand different growths.”
at temperatures up to 2,100 degrees Celsius.
The sample ingot itself starts in two pieces. The shorter
“seed” side is on the bottom and held in a base. The longer
“feed” side is suspended closely above the seed side. As the
two sides begin to melt, a small pool of liquid collects on each
surface and as they are brought closer together, the surface
tension of the pools connect to form an hour-glass-shaped
band of molten material between the seed and feed sides.
By twisting the two sides in opposite directions, the
liquid sample is effectively “stirred” to ensure a uniform
distribution of material in the melt zone. The sample is then
slowly lowered through the focused circle of light, allowing
the narrow melt zone to progressively melt, mix and solidify
its way up the feed side of the sample.
“For materials with low vapor pressure, we can grow
crystals at a rate of one millimeter per hour,” Liu said. “We
can use the technique on a variety of materials, but we
always start with the phase diagram (kind of a growth map)
to determine if it’s possible. We can’t grow crystals with high
vapor pressure or that may be toxic using this method.”
SOLUTION/FLUX GROWTH
While the other three methods work well for materials
where the crystalline outcome is known, researchers also
look to discover and grow single crystals of new binary,
ternary, quaternary or higher compounds. In many cases,
the materials in these compounds don’t melt congruently
meaning they do not melt at a single temperature.
“Solution growth is extremely versatile, and you can
often optimize and cycle through it rapidly,” said Ames
Laboratory physicist and Iowa State University
Distinguished Professor Paul Canfield. “In general, it
does not give you as large a crystal, but for basic physical
measurements, something between a millimeter and a
centimeter is more than adequate.”
In practice, the compounds for the target crystal are
combined with a material that will serve as the solution in
which the crystal compound
will dissolve. For example, to
grow a cerium-antimony crystal
from a tin solution, or flux, you
may start with four percent each
of Ce and Sb with the other 92
percent Sn.
The materials go into a
“growth” crucible that’s paired
with a “catch” crucible. These
are then sealed in a silica tube as shown (top right). The
tube assembly is placed in a furnace and heated so all the
elements melt. The temperature is then lowered closer to
the melting point of the solution element, allowing the target
crystal to form. In the Ce-Sb in Sn flux example, the initial
temperature is roughly 1,000 degrees Celsius, then lowered
to 600 degrees.
A flux-grown ytterbium-
silver-germanium crystal.
Once a crystal has formed in the growth crucible, this assem-
bly is placed in a centrifuge. Excess liquid is captured in the
catch crucible. The glass wool then traps the liquid, leaving
the crystal in the growth crucible.
GROWTH
CRUCIBLE
CATCH
CRUCIBLE
SEALED
SILICA
TUBE
Glass wool
cushions crucibles
during decanting
Glass wool in
catch crucible
captures excess
liquid during
decanting
Higher melting
element (red),
lower melting
element (green)
f the single crystal growth techniques described
in the previous article sit at one end of the materials
synthesis spectrum, then rapid solidification techniques
fall at the opposite end of the scale. The former promote
the growth of the material’s equilibrium crystalline structure.
Rapid solidification techniques promote the opposite effect,
cooling the material so quickly from liquid to solid, that the
crystals formed are small, or in some cases non-existent,
becoming amorphous or glass-like with no discernable
crystalline pattern to their overall molecular structure.
It’s also a way to form composite materials whose
constituents have widely varying “freezing” temperatures.
“If you take a molten metal and cool it, what wants to
form will vary depending on its chemistry,” said Ames
Laboratory scientist and Division of Materials Sciences and
Engineering Director Matt Kramer, “because what wants to
form is not always a homogeneous solid.”
For example, if you freeze a mixture of water and alcohol,
the water will solidify first—turning to ice—while the
alcohol remains liquid, leaving a slushy mixture until the
temperature is lowered to the alcohol’s freezing temperature.
“So when you cast a molten alloy, small crystals will form
quickly on the surface of the mold, you get segregation of
the materials and the remaining liquid becomes enriched,”
said Kramer, who is also an Iowa State University adjunct
professor of materials science and engineering, “which
results in a heterogeneous bulk material.”
Rapid solidification allows the material to cool extremely
quickly so as to suppress or even eliminate the segregation.
Techniques range from strip casting, which cools materials
at about 1,000 Kelvins per second to splat quenching which,
as the name implies, squashes a droplet of liquid material
between two plates. Splat quenching can cool the material
as high as 10
8
Kelvins per second.
“Why is that important? Because there’s an intimate
relationship between temperature and the time at which
materials cool,” Kramer said. “We call it TTT—Time-
Temperature Transformation.”
It takes a certain finite amount of time for the initial
crystals to form, a process called nucleation. The molten
material has to organize itself into crystals only a few 10s of
atoms across and then those crystals need to grow.
“There’s a very non-linear relationship between time
and temperature transformation,” Kramer continued.
“Solidification occurs over a broad range of temperatures.
At too high a temperature, it stays molten. At a temperature
just below the melting temperature, the material solidifies
slowly, and in cases where constituents have different
melting temperatures, significant segregation in the casting
can occur if cooled slowly
Rapid solidification techniques allow researchers to
bypass the time-temperature transformation so a molten
metal alloy forms without a crystalline order, creating a
metallic glass.
“Glassy metals have some very unusual properties,”
Kramer said. “On average, they tend to have very good
strength, but not much plasticity, so they are hard to mold
into shapes.”
However, by first forming a metallic glass, then heating
the material back up, researchers can achieve metastable
phases of the material that aren’t attainable by other methods,
such as casting. And these intermediate phases may have
desirable properties such as strength, ductility, resistivity, or
conductivity.
“Manipulating the phases, their sizes, the degree
at which we can control their growth, and even their
morphology, or shapes, are all buried in the details of the
classical time-temperature transformation,” Kramer said.
“A lot of the work we’re doing is trying to understand the
relative balance of cooling rates to phase selection process.
How can we predict and control those so we can move
beyond an Edisonian approach.”
Researchers at Ames Laboratory use several techniques
B Y K E R R Y G I B S O N
Frozen in a Flash
Ames Laboratory scientist Brandt Jensen loads a sample into
the melt spinner. The induction coil melts the sample, which
is then forced in a stream onto the spinning copper wheel.
I
RAPID SOLIDIFICATION KEEPS MATERIALS ON COOLING FAST TRACK