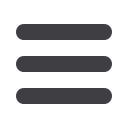
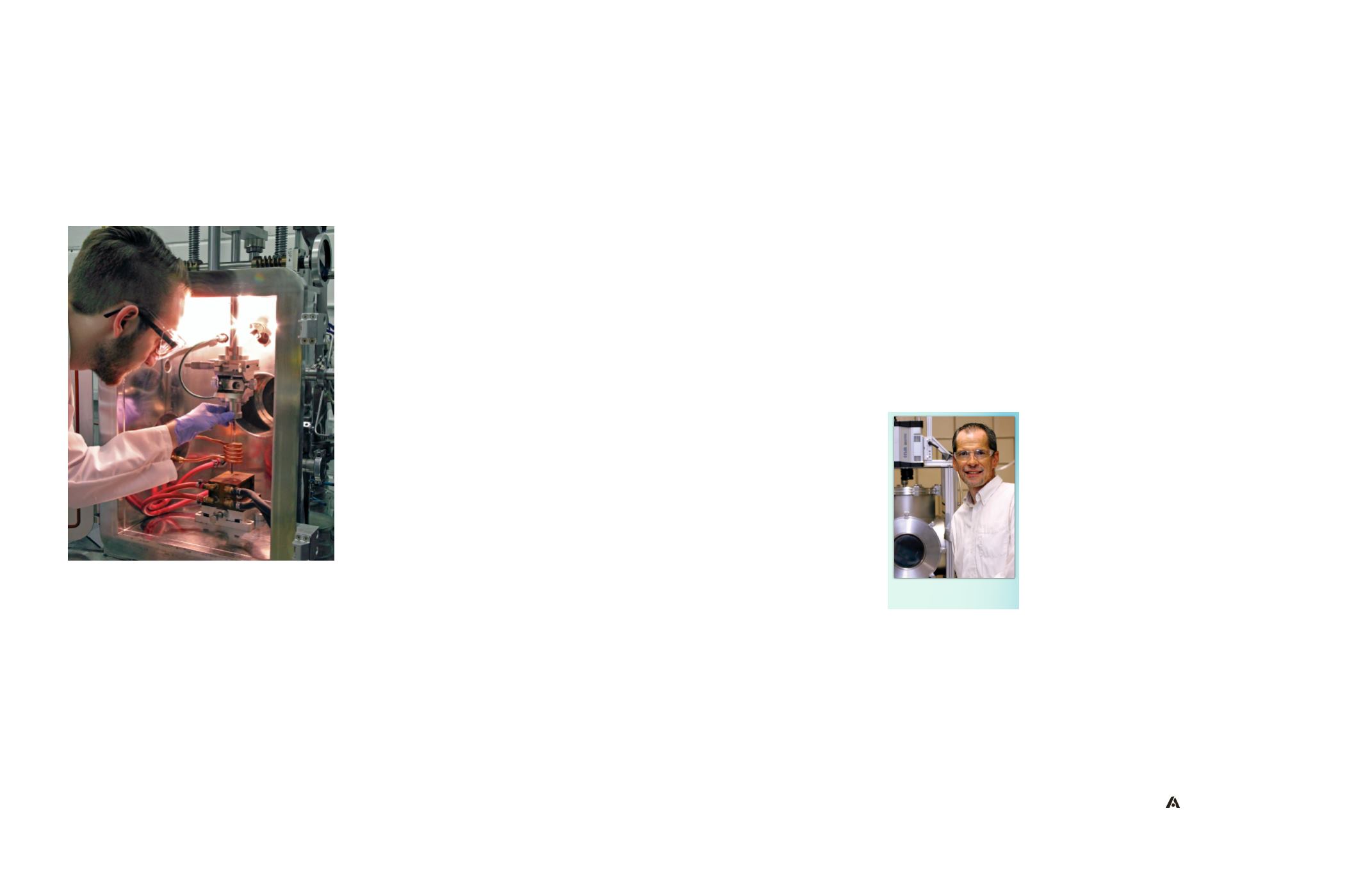
12
Inqui r y I s sue
1
| 2016
Inqui r y I s sue
1
| 2016
13
including melt spinning, injection casting, and high-pressure
gas atomization (covered separately on pages 6-7) to produce
small-grained and amorphous materials.
MELT SPINNING
This technique involves shooting a stream of molten
material onto a spinning copper wheel where it solidifies
quickly, forming a ribbon of metal. The copper wheel is
typically water cooled and depending on the speed at which
it spins, up to 30 meters per second, the molten metal is
quenched up to 10
6
Kelvins per second.
“There are limits to the process,” said Ames Laboratory
scientist and ISU associate professor of materials science
and engineering Jun Cui. “The copper wheel must be
perfectly balanced to spin at such high speeds. And
beyond a certain point, the material no longer flows in a
ribbon but breaks apart.”
There is also a variation in the process where the copper
wheel has small grooves cut across its surface. These grooves
intentionally break the cooled metal into short strips, which
Cui said are easier to work with in some applications.
INJECTION CASTING
As the name implies, injection casting forces the molten
material into a copper mold, typically a small cylinder that
will produce short rods one to four millimeters in diameter.
The mold is held inside a larger water-cooled copper mold
providing quench rates fast enough to produce amorphous
(glassy) samples in some alloys.
“Small samples—usually less than five grams—are
placed in a graphite or quartz nozzle and rapidly heated by
induction to several hundred degrees above the melting
point,” said Matt Besser, Ames Laboratory scientist and
manager of the Laboratory’s Materials Preparation Center.
“We then drop it out of the heating zone and pressurize the
system so the material squirts into the mold.”
By using different shaped molds, material can be cast in
plates, or wedges. Besser said thermocouples can be placed
along the length of the wedge to measure the difference in
cooling rates from the fastest at the thin tip to the slowest at
the thicker end.
“We’re able to fabricate samples to fit specific needs,”
Besser said, “and it’s convenient because we can produce
small samples, especially when the alloy contains
expensive materials.”
One of the most common and robust ways to create a
new material, particularly a metallic alloy, is to melt two or
more constituent materials, mix them in the liquid state,
then freeze or “solidify” them under certain controlled
conditions. While seemingly simple, solidification processing
can produce an incredible variety of material structures
with important features on scales from nanometers to
centimeters, giving rise to a host of remarkable properties
ranging from enhanced strength and stiffness to unusual
magnetic, thermal, electrical, and photonic properties.
But the make-up and structure, and therefore the
properties, of that end result can vary greatly depending on a
variety of conditions present as the material transitions from
liquid to solid. Ames Laboratory scientist Ralph Napolitano
works to explain and predict what takes place at that liquid-
solid interface and how those various interactions result in
certain structures, chemistries and properties.
“When a material goes from a liquid to a solid phase, a lot
of things must happen as part of that transformation,” said
Napolitano, who is also an Iowa State University professor of
materials science and engineering. “Nominally speaking, an
amorphous or non-crystalline liquid phase has to reconfigure
itself into some kind of crystalline packing. But many other
simultaneous events are taking place to make that happen.
Indeed, it is the way that the different transport processes
and different structural entities enter into that equation that
really influences what that final structure may look like.”
If equilibrium yields the normal or expected result,
there are all kinds of deviations that can shift the result
from equilibrium. Some of them are very small deviations,
such as slightly different chemical compositions or
slightly different concentrations of different kinds of
crystalline defects. Deviations can also be very large—
completely different crystalline packing or composition
or even an array of multiple phases that you might never
see closer to equilibrium.
“What dictates how far away from the final equilibrium
state you might be is what happens along that pathway
from the equilibrium liquid to this far-from-equilibrium
structure,” Napolitano said. “Varying the composition of
a material and the rate at which we cool it has dramatic
influence over final phase or assembly.”
“Beyond just the phase—the particular crystalline
structure—conditions during freezing greatly influence the
growth morphology,” he continued. “Any given phase will
growwith a certainmorphology that is dynamically optimized
with respect to all of the different processes—such as the
redistribution of heat, chemical species, and configuration
of crystalline defects—making the overall transformation
more efficient. Composition and cooling rate, along with
the phase itself and the energies of the crystal defects
and interfaces, all play a role in this collective dynamical
optimization, ultimately resulting in the selection of the final
state, which may look nothing like the equilibrium state.
“This far-from-equilibrium
synthesis provides a portal
or pathway to structures,
chemistries, and properties
that aren’t accessible through
conventional
methods,”
Napolitano said.
To complicate matters,
these pathways may include
several other steps —before
and after solidification, so
that the complex freezing
structure may only serve
as some intermediate stage,
along the way to a desired
structure.
Cooling rate provides a high level of control in certain
windows. At the low (slow) end, cooling rate can be
controlled very carefully, and even cooling rates from
isothermal treatments to 100 degrees per second can be
controlled reasonably well.
“We can go to cooling rates of 10
3
to 10
4
degrees per
second with techniques like melt spinning, but within that
window, process control is challenging and local variations
exist,” Napolitano said. “We have investigated such
variations, and our understanding has certainly increased.
Even so, with relatively few ‘process knobs’ to turn (e.g. melt
temperature, wheel speed, wheel material, injection rate
and stream diameter) precise quantitative control remains
a real challenge.”
Seeking explanations for
solidification puzzles
Jacob Fischer, undergraduate research assistant, loads a
sample into the injection casting system. The melted mate-
rial is injected into water-cooled copper molds.
As a strategy to reveal a clearer picture of the complex
behaviors, Napolitano’s group has chosen to focus on a few
select two-component or “binary” systems. In particular,
binary systems, such as copper-zirconium and aluminum-
samarium, provide great opportunities to investigate far-
from-equilibrium transformation. These systems exhibit
complex competitive solidification, glass formation, and
crystallization, forming a host of non-equilibrium phases and
multi-scale growth structures. At the same time, with only
two components, analytical and computational treatment of
the thermodynamics and kinetics become more tractable,
compared with multi-component systems.
“With both of these systems, there’s a composition
range over which the liquid forms a glass rather easily so
you can cool it at rates that are achievable experimentally,”
Napolitano said. “Once the alloy is glassy, other treatments
can be used to crystalize the material at low temperature.
In this regime, conditions can be controlled carefully, and
reactions can be slowed substantially, even permitting in-
situ real-time investigation. Of course, having an accurate
and comprehensive picture of the system thermodynamics
is critical. Whether you’re solidifying the material directly
from a liquid, or first quenching to a glass and then
heating to crystallize the material, you still have that same
thermodynamic playing field.”
The aluminum-samarium work is being expanded to a
larger range of binaries, including other aluminum-rare earth
alloys. In general, those systems are expected to exhibit
similar behaviors, though Napolitano warns that very subtle
effects can dramatically tip the balance between phases
and growth structures. Very small energetic differences
exist between the competing phases. Under high driving
forces, these differences are often negligible and the kinetic
pathways control the outcome. Even changes in chemical
composition on the order of a percent or less can dramatically
change the final state.
“This kind of study is only possible by bringing together
many different approaches in theoretical condensed matter
physics, materials science, computational thermodynamics,
materials synthesis, and state-of-the-art characterization,”
Napolitano said. “There is no doubt that this work requires
the full gamut of experimental and computational capability
and a team of investigators with a broad range of expertise.”
To that end, the new electron microscopy equipment at
Ames Laboratory’s Sensitive Instrument Facility (SIF) will
play a vital role.
“It’s important not only in terms of spatial resolution,
but some of the in situ capabilities as well,” he said. “Hot-
stage transmission electron microscopy with atomic scale
resolution will allow us to look at some of the early stage
dynamics that really are watershed events that tend to send
the material down a whole different trajectory. So absolutely,
the SIF is critical to moving forward in this area.”
Ralph Napolitano